CNC Table Build
Function: To create a machine which allows me to manufacture and prototype projects and prototypes in wood, foam, and metal.
Inspiration: I love to prototype and design, but at times 3D printing isn’t strong or fast enough. I wanted a way to be able to design and create in other materials in an easy way.
Methods: Build from scratch. In progress: so far I have finished the motion system (build around 20mm linear rails) and finished the belt layout and electronics box. Still need to fabricate a custom steel bracket for the Z axis, as I have about 2mm of deflection over the 500mm Z.
Update: Have decided to go in a new direction. I realized that our previous design wouldn’t be strong enough to mill aluminum, and some hardwoods. I have ordered new parts and am building around 20mm Hiwin linear rails, to ensure the entire system is stable and responsive. These will be arriving Jan/Feb and I will begin work ASAP.
Added linear rails, rebuilt system around 25mm thick 6061 aluminum plates, much more sturdy. Still have to work out how to mount the lefthand ball screw for the Y axis, as the mounting system was designed by an idiot (me), and the bolts need to be inserted from the inside, which has just over 2mm of clearance from the linear rail- not early enough to insert and tighten a bolt, much less for the bolt head.
Have ordered a new lefthand X gantry plate, this time with pockets milled in order to recess the bolt heads and also with a new mounting design to allow me to mount the ball screw before mounting the plate to the linear rails.
Successful test run. Continue to test capabilities and fine-tune.
Outcome: Still working on securing small details and parts, things like air and coolant lines need to be bundled and properly setup, instead of hanging in the dead space under the machine The lefthand ball screw setup still eludes me, and I need to find a better way of mounting it to the X gantry.
Failures and challenges:
My original budget for this project only allowed for an $80 motion system. After securing funding for the project (a combo of my money and donations from family members), I changed the scope of the build to allow for a larger build volume. This increase the cost of the project and the weight of the table. I made the mistake of sticking with the original $80 motion system when in fact I needed a much nicer linear rail based system. I completely overlooked this issue and had to spend hundreds more (over budget) on new rails.
Successful test run October ‘21
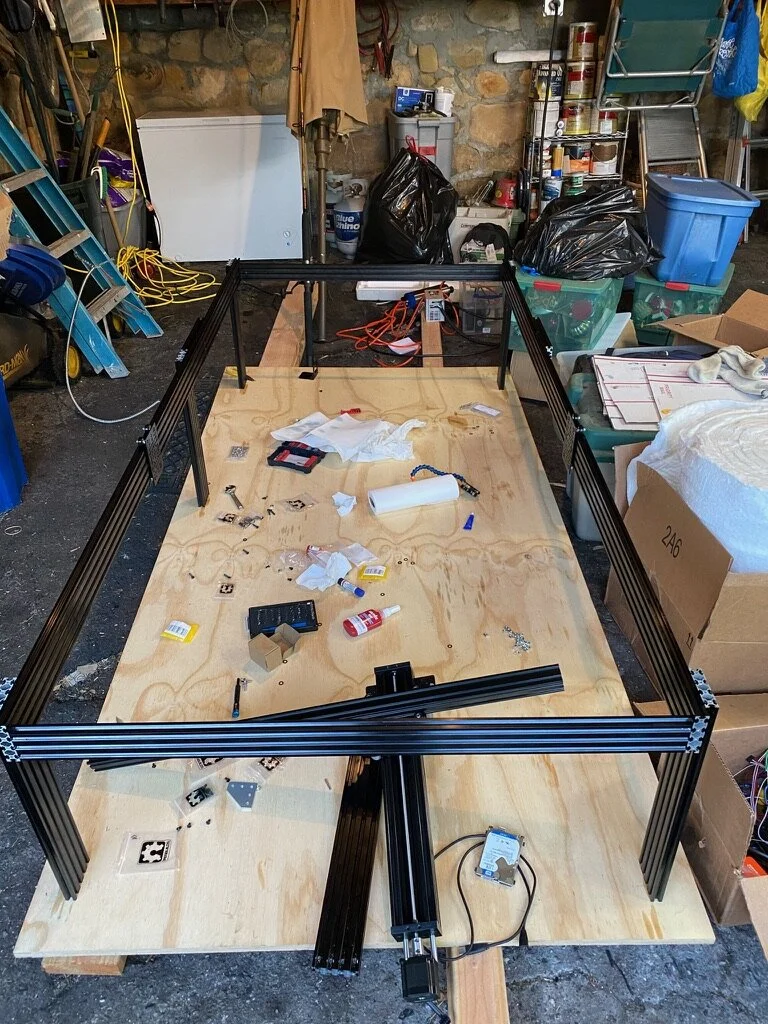
Basic CNC frame
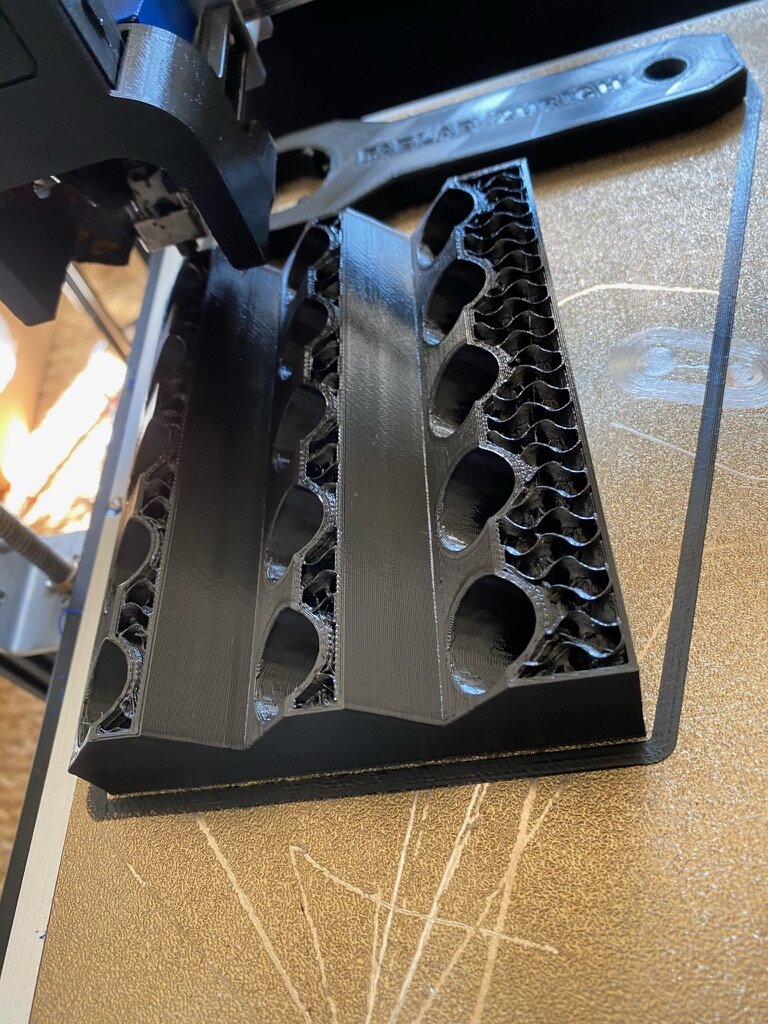
Printing a mount for the spindle
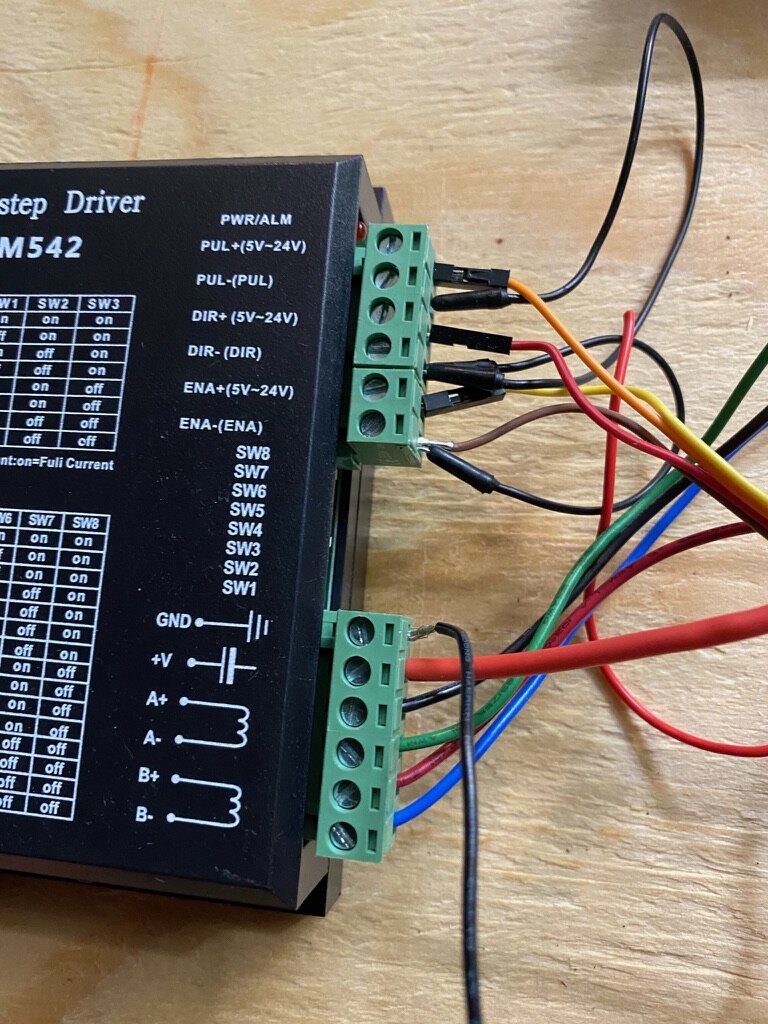
Wiring the stepper drivers
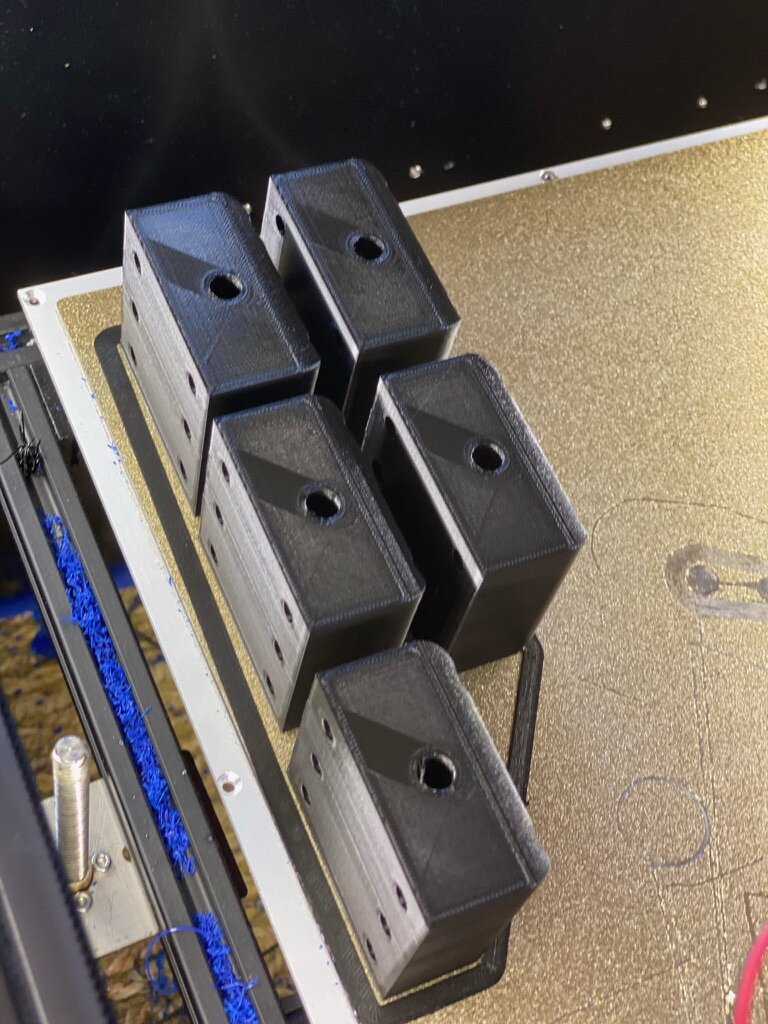
Printed blocks for belt supports
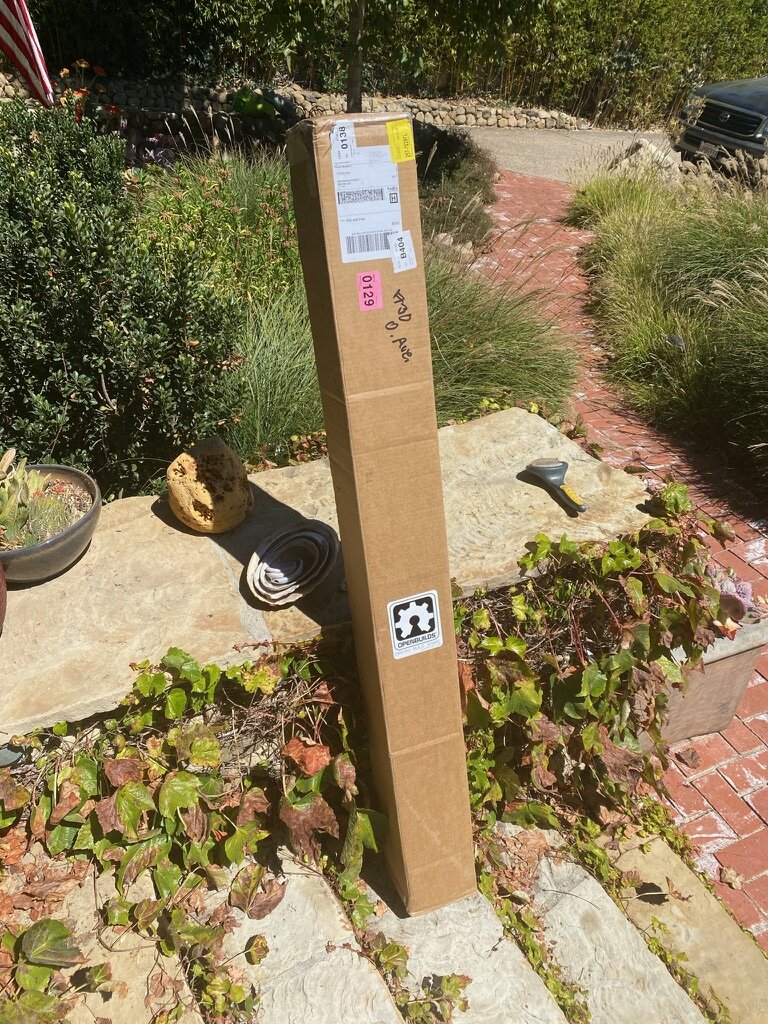
The aluminum extrusions for the frame

The spindle in its beat up box
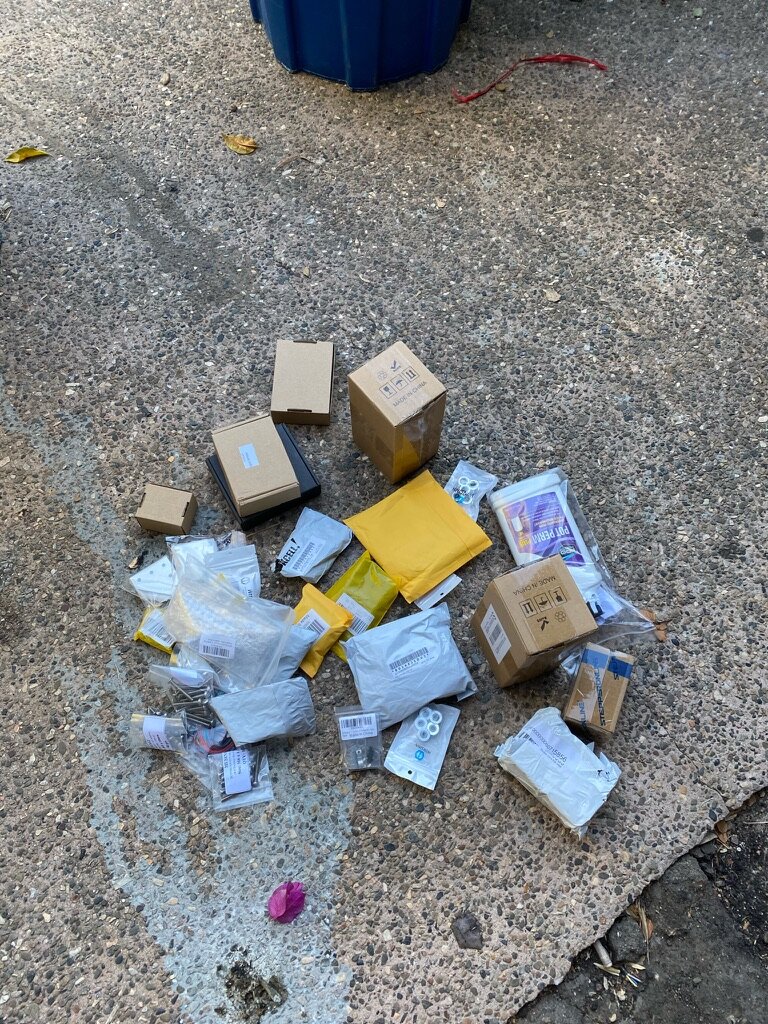
Assorted components
The spindle- It weights almost 10kg

Hiwin HGW20 blocks- they weigh almost 0.8kg each!

Attaching the x-axis linear rails

view of the y and x axis linear rails
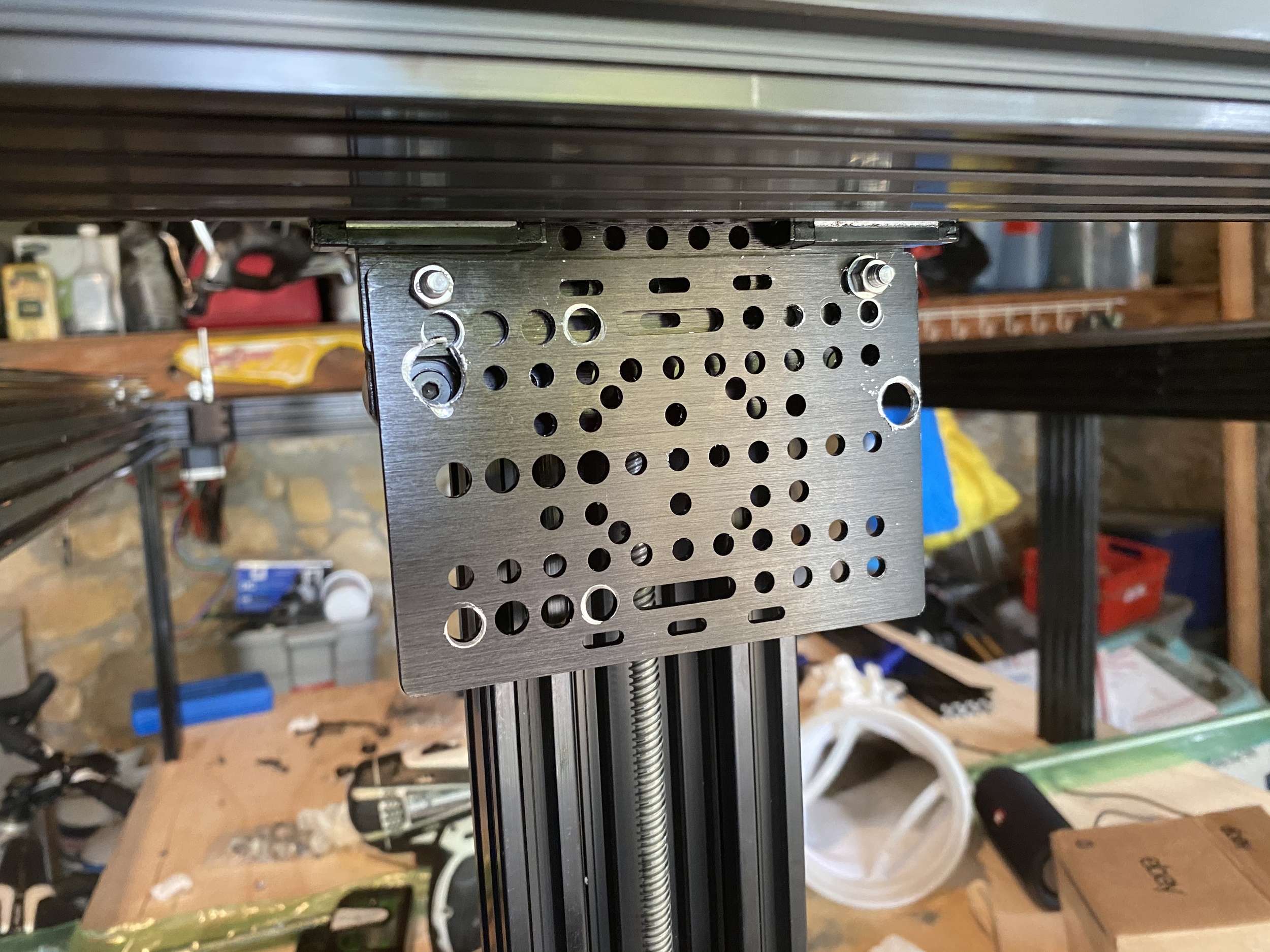
test plate for the belt system

Custom Made X-Axis (Can support up to 300kg)

Stock for Our Two X Brackets- 1"x8"x18" each (Banana For Scale)
New Cable drag Chain

Custom cables (ignore the so so soldering job)

Wiring the stepper drivers

The new completed x axis
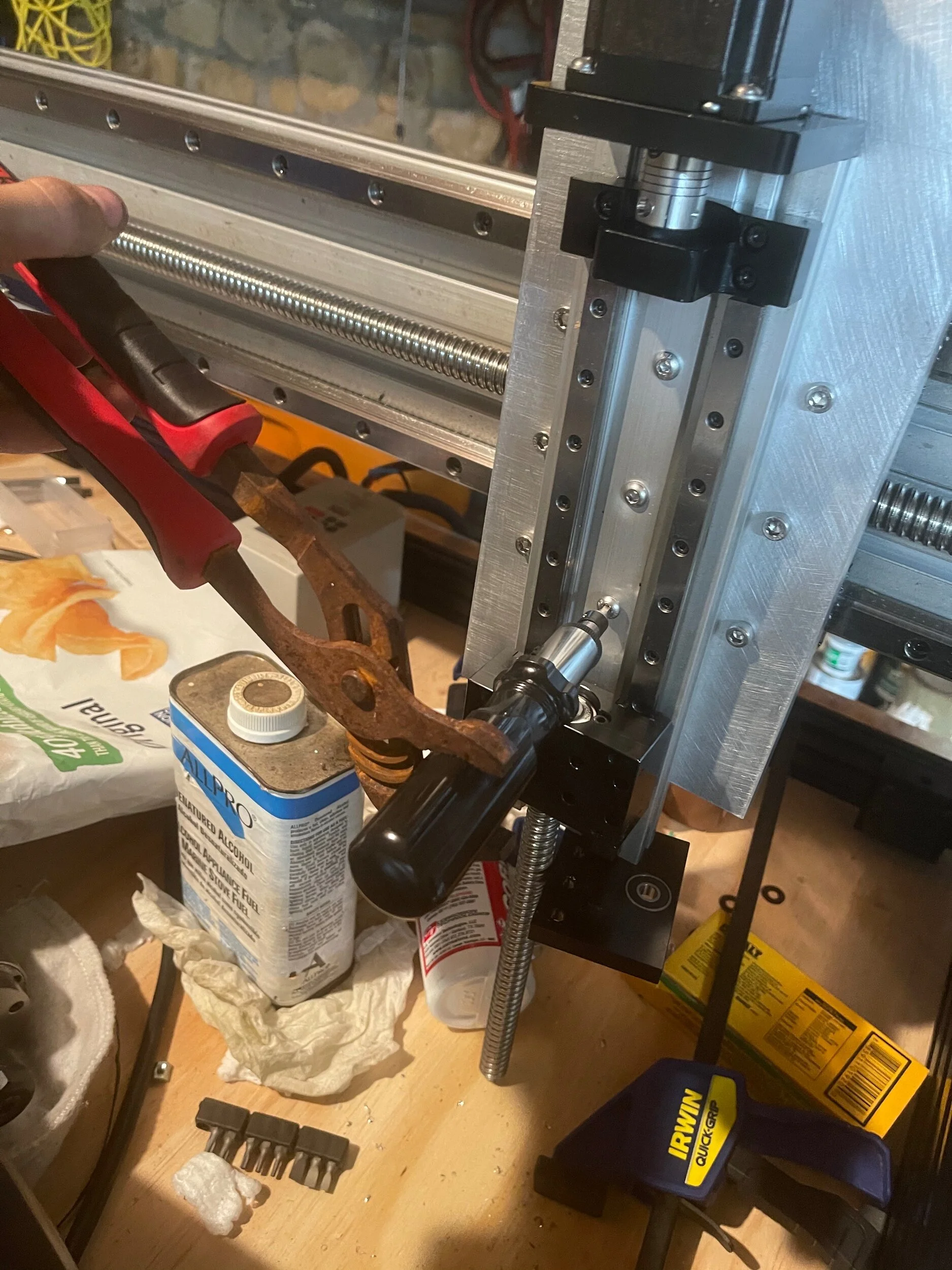
Is this how you tighten a bolt?
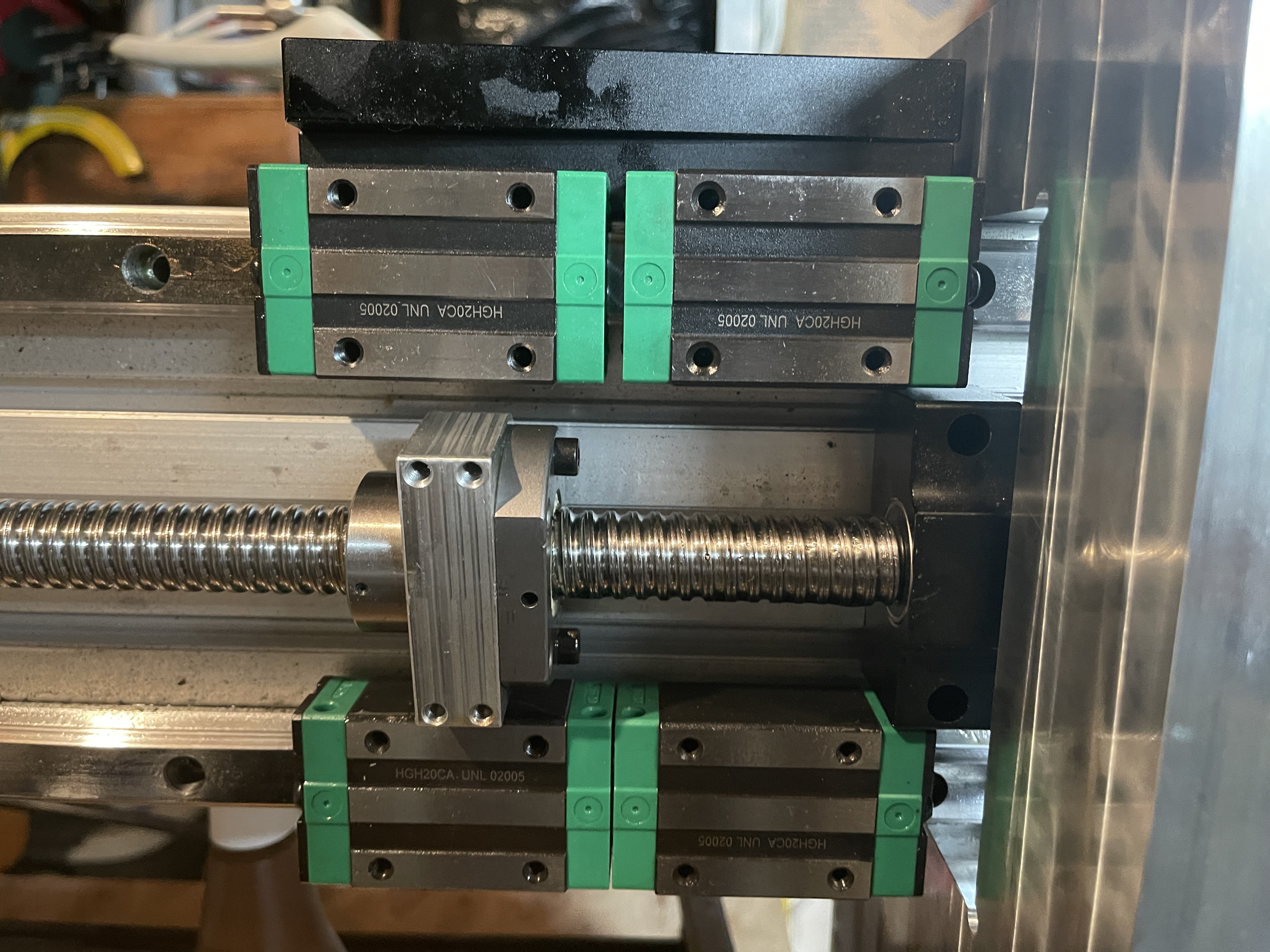
Aligning the x axis rails
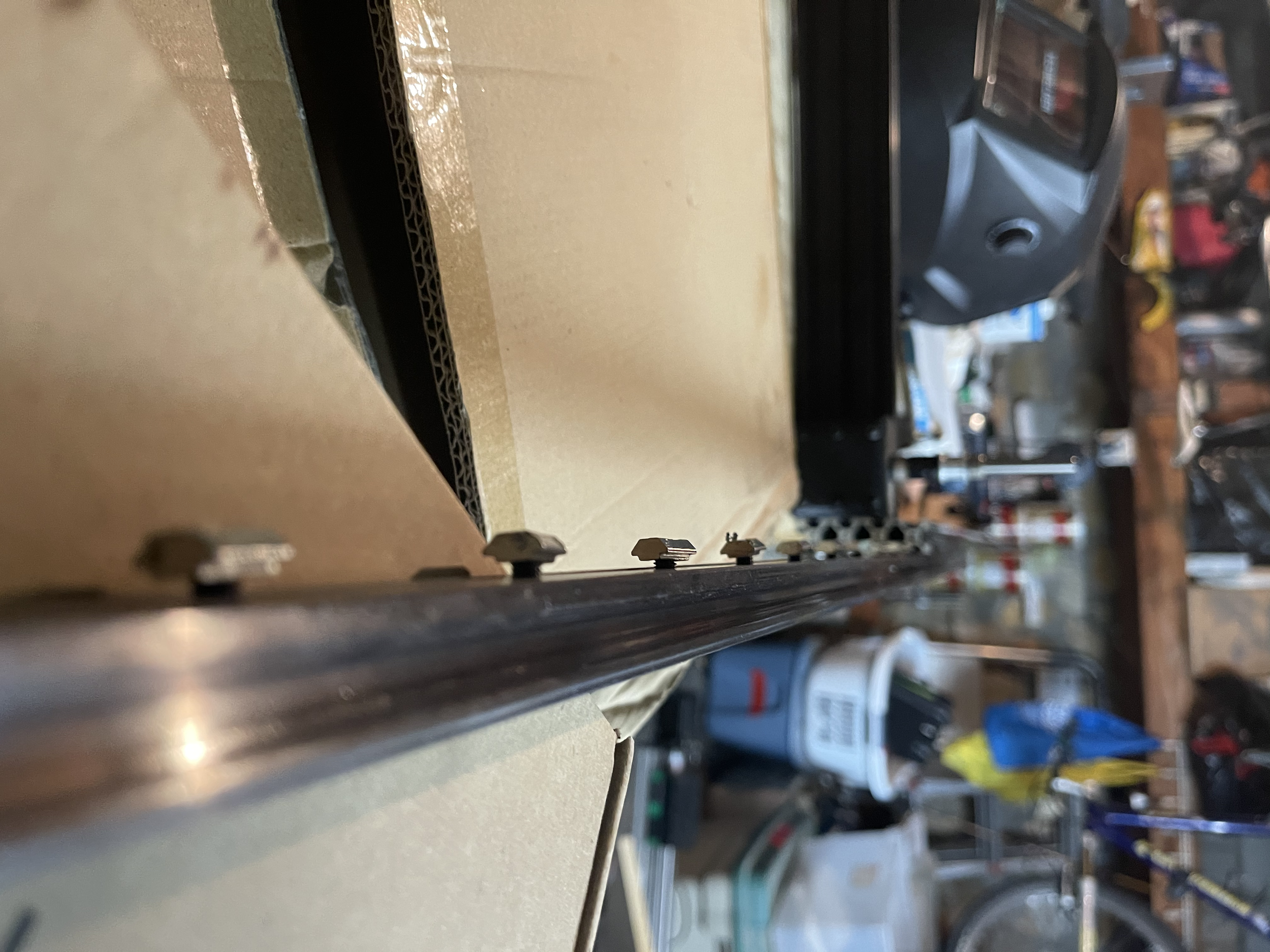
Need to insert ever t nut perfectly or the rails seizes up

Inserting the Y axis rails. Not easy to insert

X axis gantry plates
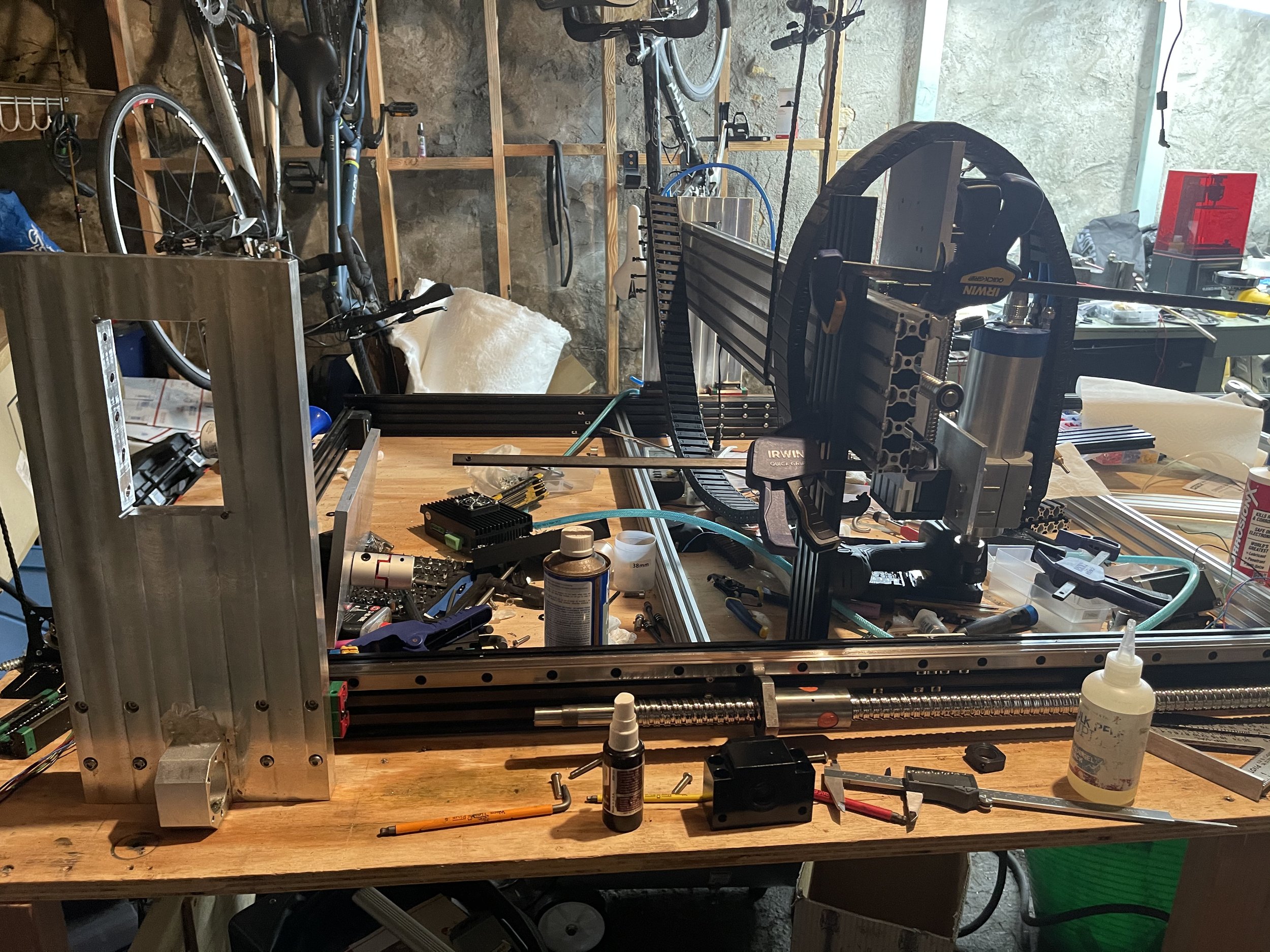
Mounting the X gantry plates
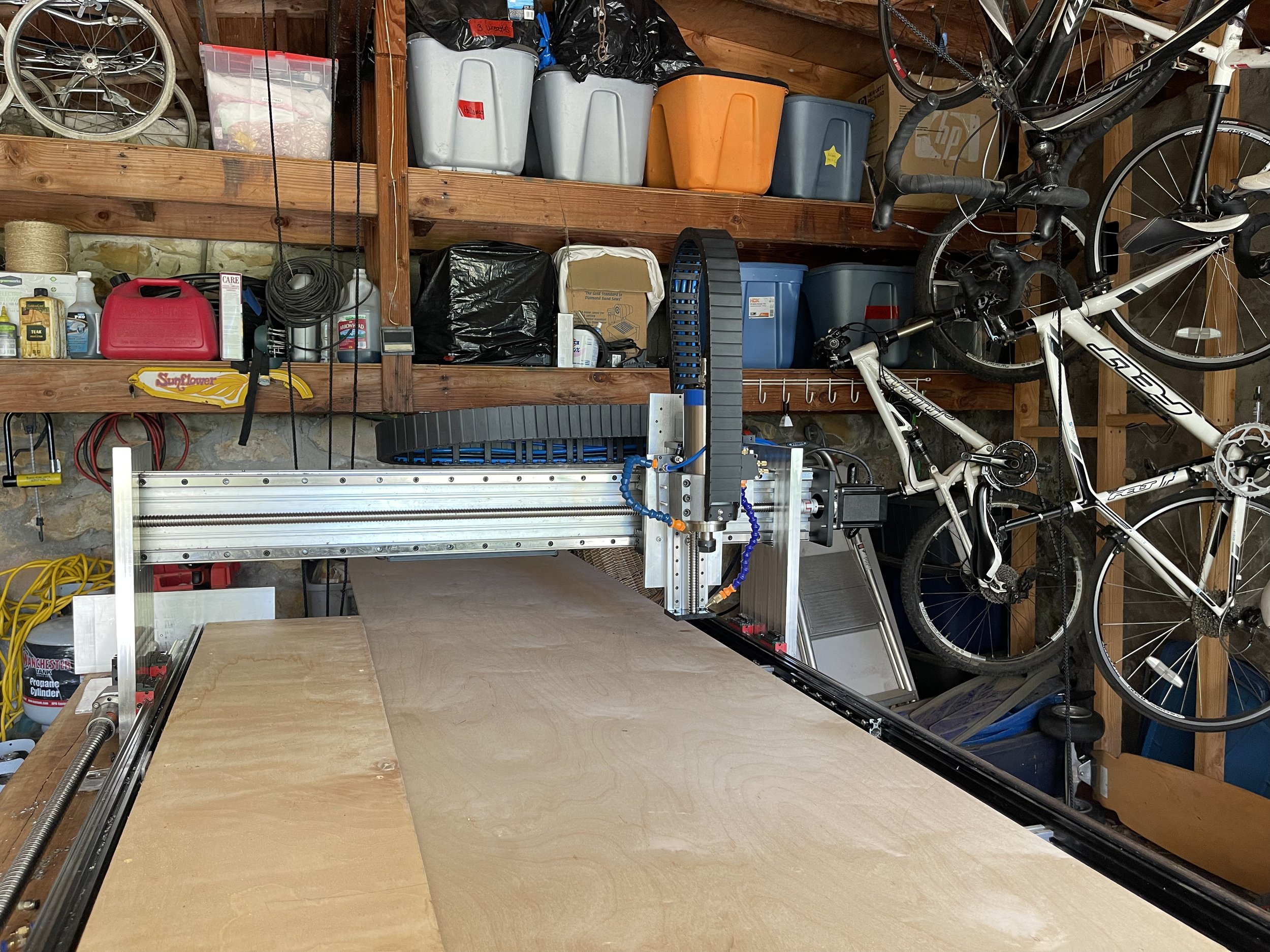
(Semi) completed CNC, minus the left ball screw and assorted hoses and fluid lines
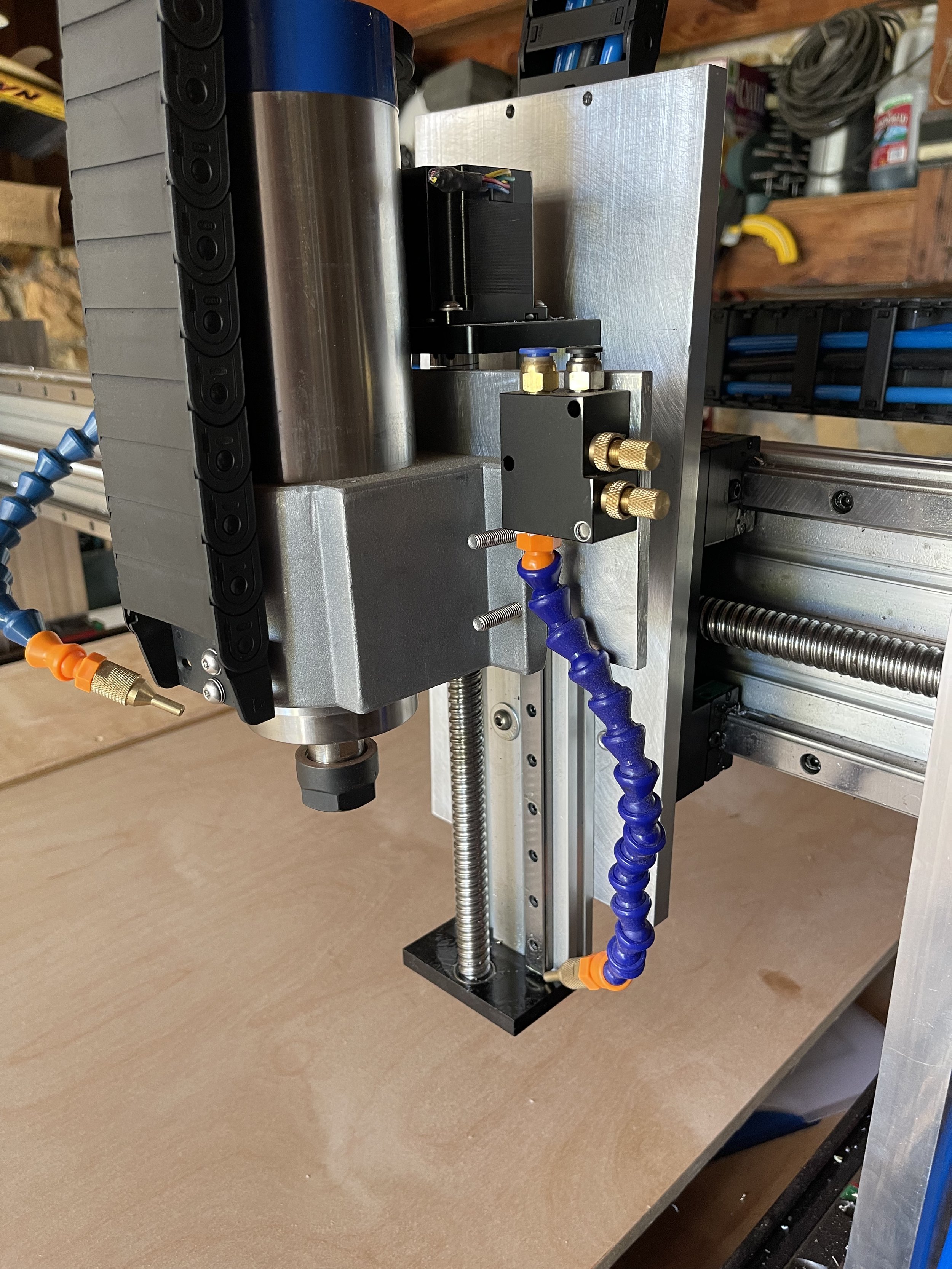
The Z axis and spindle